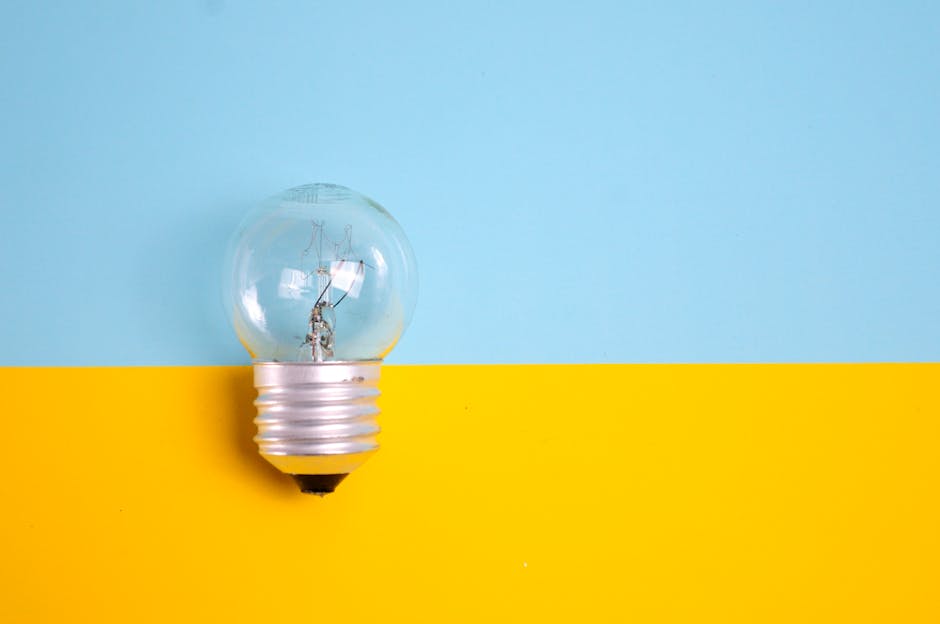
W obliczu rosnących cen energii i coraz bardziej wymagających regulacji środowiskowych, efektywność energetyczna staje się strategicznym priorytetem dla przedsiębiorstw przemysłowych. Sektor przemysłowy odpowiada za około 1/3 globalnego zużycia energii, co oznacza, że optymalizacja wykorzystania energii może przynieść zarówno znaczące oszczędności finansowe, jak i realne korzyści dla środowiska. W niniejszym artykule przedstawiamy kompleksowe podejście do efektywności energetycznej w przemyśle, strategie jej wdrażania oraz najnowsze technologie i rozwiązania.
Dlaczego efektywność energetyczna jest kluczowa dla przemysłu?
Efektywność energetyczna to nie tylko kwestia ekologii, ale przede wszystkim biznesowa konieczność. Oto główne powody, dla których firmy przemysłowe powinny priorytetowo traktować optymalizację zużycia energii:
Redukcja kosztów operacyjnych
Koszty energii stanowią znaczną część kosztów operacyjnych w przemyśle, szczególnie w branżach energochłonnych jak hutnictwo, przemysł chemiczny czy papierniczy. W niektórych przypadkach mogą sięgać nawet 40% całkowitych kosztów produkcji. Skuteczne zarządzanie energią może przynieść oszczędności rzędu 10-30%, co bezpośrednio przekłada się na poprawę rentowności przedsiębiorstwa.
Spełnienie wymogów regulacyjnych
Unia Europejska wprowadza coraz bardziej restrykcyjne regulacje dotyczące efektywności energetycznej i emisji gazów cieplarnianych. Dyrektywa o efektywności energetycznej (EED) nakłada na duże przedsiębiorstwa obowiązek przeprowadzania audytów energetycznych co cztery lata lub wdrożenia certyfikowanego systemu zarządzania energią. Nieprzestrzeganie tych wymogów może skutkować karami finansowymi.
Zrównoważony rozwój i odpowiedzialność społeczna
Konsumenci i inwestorzy coraz częściej zwracają uwagę na środowiskowe i społeczne aspekty działalności firm. Przedsiębiorstwa, które aktywnie redukują swój ślad węglowy poprzez efektywność energetyczną, mogą poprawić swój wizerunek rynkowy i przyciągnąć zarówno świadomych klientów, jak i inwestorów zainteresowanych ESG (Environmental, Social, Governance).
"Efektywność energetyczna to najtańsze, najczystsze i najbardziej dostępne źródło energii. To pierwsze paliwo transformacji energetycznej." - Fatih Birol, Dyrektor Wykonawczy Międzynarodowej Agencji Energetycznej (IEA)
Strategie poprawy efektywności energetycznej w przemyśle
Efektywne zarządzanie energią w przedsiębiorstwie przemysłowym wymaga systemowego podejścia i długofalowej strategii. Oto kluczowe elementy takiego podejścia:
1. Audyt energetyczny jako punkt wyjścia
Pierwszym krokiem w kierunku poprawy efektywności energetycznej jest kompleksowy audyt energetyczny, który pozwala zidentyfikować główne obszary zużycia energii, nieefektywne procesy i urządzenia oraz potencjał oszczędności. Profesjonalny audyt energetyczny obejmuje:
- Analizę historycznego zużycia energii
- Szczegółowy przegląd procesów produkcyjnych
- Inspekcję instalacji i urządzeń
- Identyfikację potencjalnych usprawnień
- Oszacowanie kosztów i korzyści proponowanych rozwiązań
- Opracowanie planu działania z priorytetyzacją inwestycji
Audyt energetyczny powinien być przeprowadzany przez wykwalifikowanych specjalistów, którzy posiadają doświadczenie w danej branży przemysłowej i znają specyfikę procesów produkcyjnych.
2. Wdrożenie systemu zarządzania energią
System zarządzania energią (SZE) zgodny z normą ISO 50001 zapewnia strukturę i metodologię ciągłego doskonalenia efektywności energetycznej. Kluczowe elementy systemu obejmują:
- Politykę energetyczną firmy i jasno określone cele
- Strukturę organizacyjną z określonymi rolami i odpowiedzialnościami
- System monitorowania i pomiaru zużycia energii
- Regularne przeglądy energetyczne
- Plany działania i programy poprawy
- Szkolenia i budowanie świadomości pracowników
Certyfikowany system ISO 50001 nie tylko pomaga systematycznie obniżać zużycie energii, ale również spełnia wymogi regulacyjne dotyczące obowiązkowych audytów energetycznych.
3. Zaawansowany monitoring i analityka energetyczna
Nie można zarządzać tym, czego nie można zmierzyć. Nowoczesne systemy monitoringu energetycznego pozwalają na szczegółową analizę zużycia energii w czasie rzeczywistym, identyfikację anomalii i optymalizację procesów. Kluczowe funkcje takich systemów to:
- Pomiar zużycia energii na poziomie poszczególnych maszyn i linii produkcyjnych
- Wizualizacja danych w czasie rzeczywistym
- Analityka predykcyjna wykrywająca potencjalne problemy
- Automatyczne alerty o odchyleniach od norm
- Benchmarking wewnętrzny i zewnętrzny
- Generowanie raportów i wskaźników efektywności (KPI)
Zaawansowana analityka energetyczna wykorzystująca sztuczną inteligencję i uczenie maszynowe może identyfikować wzorce zużycia energii niedostrzegalne dla człowieka i sugerować optymalne parametry procesów produkcyjnych.
Technologie i rozwiązania poprawiające efektywność energetyczną
Istnieje szereg technologii i rozwiązań, które mogą znacząco poprawić efektywność energetyczną w różnych obszarach działalności przemysłowej:
Modernizacja napędów elektrycznych
Silniki elektryczne odpowiadają za około 70% zużycia energii elektrycznej w przemyśle. Zastosowanie wysokosprawnych silników (klasy IE3 lub IE4) oraz napędów o zmiennej częstotliwości (VFD) może przynieść oszczędności energii rzędu 20-50%. VFD pozwalają na precyzyjne dostosowanie prędkości silnika do faktycznych potrzeb procesu, eliminując straty energii występujące przy pracy z pełną mocą.
Odzysk ciepła odpadowego
W wielu procesach przemysłowych generowane są znaczne ilości ciepła odpadowego, które często jest uwalniane do atmosfery. Systemy odzysku ciepła pozwalają na wykorzystanie tego ciepła do innych procesów, ogrzewania pomieszczeń czy wstępnego podgrzewania wody. Technologie odzysku ciepła obejmują:
- Wymienniki ciepła dla gazów spalinowych
- Systemy ORC (Organic Rankine Cycle) do produkcji energii elektrycznej z niskotemperaturowego ciepła odpadowego
- Pompy ciepła przemysłowe
- Rekuperatory i regeneratory
Efektywny odzysk ciepła może obniżyć zapotrzebowanie na energię pierwotną nawet o 15-20% w energochłonnych branżach.
Optymalizacja systemów sprężonego powietrza
Systemy sprężonego powietrza są jednymi z najmniej efektywnych energetycznie instalacji w przemyśle - tylko około 10-15% energii elektrycznej zużywanej przez sprężarki jest efektywnie wykorzystywane. Kluczowe usprawnienia obejmują:
- Uszczelnienie instalacji i eliminację wycieków (które mogą odpowiadać za 20-30% zużycia energii)
- Optymalizację ciśnienia roboczego (obniżenie o 1 bar może zmniejszyć zużycie energii o 7-10%)
- Zastosowanie sprężarek z regulacją prędkości
- Odzysk ciepła ze sprężarek (do 90% energii elektrycznej jest zamieniane na ciepło)
- Inteligentne systemy sterowania kaskadowego wieloma sprężarkami
Modernizacja systemów oświetleniowych
Choć oświetlenie nie jest największym konsumentem energii w przemyśle, jego modernizacja jest relatywnie łatwą i szybko zwracającą się inwestycją. Zastąpienie tradycyjnych źródeł światła oprawami LED wraz z inteligentnymi systemami sterowania (czujniki obecności, regulacja jasności zależna od światła dziennego) może przynieść oszczędności energii na poziomie 50-80%.
Kogeneracja i trigeneracja
Skojarzona produkcja energii elektrycznej i ciepła (CHP - Combined Heat and Power), a w przypadku trigeneracji również chłodu, pozwala na znacznie bardziej efektywne wykorzystanie paliwa pierwotnego. Podczas gdy konwencjonalna elektrownia osiąga sprawność rzędu 33-35%, systemy kogeneracyjne mogą wykorzystać nawet 80-90% energii zawartej w paliwie. Rozwiązania te są szczególnie opłacalne dla zakładów o dużym i stabilnym zapotrzebowaniu na ciepło procesowe.
Case study: Skuteczne wdrożenie efektywności energetycznej w hucie szkła
Jednym z przykładów udanego wdrożenia kompleksowego programu efektywności energetycznej jest huta szkła w województwie śląskim, która w ciągu trzech lat zdołała zredukować zużycie energii o 23%, osiągając roczne oszczędności na poziomie 3,5 mln złotych.
Kluczowe elementy projektu obejmowały:
- Instalację systemu monitoringu energetycznego obejmującego 120 punktów pomiarowych
- Modernizację pieców topliwych i wdrożenie zaawansowanego sterowania procesem topienia szkła
- Odzysk ciepła z gazów odlotowych do podgrzewania wsadu
- Wymianę starych sprężarek na nowoczesne jednostki z regulacją prędkości
- Wdrożenie systemu zarządzania energią zgodnego z ISO 50001
- Program szkoleniowy dla pracowników i system motywacyjny nagradzający pomysły związane z oszczędnością energii
Okres zwrotu z inwestycji w przypadku tego projektu wyniósł 2,3 roku, a dodatkowym efektem była redukcja emisji CO2 o 15 000 ton rocznie.
Finansowanie projektów efektywności energetycznej
Dla wielu przedsiębiorstw barierą we wdrażaniu projektów efektywności energetycznej są ograniczenia budżetowe. Istnieje jednak szereg mechanizmów finansowania takich inwestycji:
Białe certyfikaty
System świadectw efektywności energetycznej (tzw. białych certyfikatów) pozwala na uzyskanie wymiernych korzyści finansowych za realizację przedsięwzięć służących poprawie efektywności energetycznej. Po zakończeniu inwestycji przedsiębiorstwo może ubiegać się o przyznanie certyfikatów, które następnie może sprzedać na Towarowej Giełdzie Energii.
Finansowanie przez ESCO
Model ESCO (Energy Service Company) pozwala na realizację projektów bez angażowania własnych środków finansowych. Firma ESCO finansuje i realizuje projekt, a następnie otrzymuje wynagrodzenie z osiągniętych oszczędności energii. Po zakończeniu kontraktu, który zwykle trwa 5-10 lat, wszystkie korzyści z efektywności energetycznej trafiają do przedsiębiorstwa.
Fundusze i programy UE
W ramach Europejskiego Zielonego Ładu i Funduszu Odbudowy dostępne są znaczące środki na projekty związane z poprawą efektywności energetycznej. W Polsce operatorem wielu programów jest Narodowy Fundusz Ochrony Środowiska i Gospodarki Wodnej, który oferuje zarówno dotacje, jak i preferencyjne pożyczki.
Wyzwania i bariery we wdrażaniu efektywności energetycznej
Mimo oczywistych korzyści, wdrażanie efektywności energetycznej w przemyśle napotyka na szereg wyzwań:
Bariery organizacyjne
- Niedostateczna świadomość zarządu i pracowników
- Brak jasno określonych ról i odpowiedzialności
- Opór przed zmianami w ugruntowanych procesach
- Niedostateczna komunikacja między działami technicznymi i finansowymi
Bariery finansowe
- Konkurencja o środki inwestycyjne z projektami bezpośrednio produkcyjnymi
- Zbyt krótkie wymagane okresy zwrotu z inwestycji (często poniżej 2 lat)
- Brak uwzględnienia pełnych korzyści (np. redukcja kosztów utrzymania, poprawa jakości)
- Trudności w pomiarze i weryfikacji oszczędności
Bariery techniczne
- Obawy o wpływ na ciągłość i jakość produkcji
- Brak specjalistycznej wiedzy technicznej
- Trudności z integracją nowych technologii z istniejącymi systemami
- Niepewność co do faktycznych oszczędności w specyficznych warunkach zakładu
Przyszłość efektywności energetycznej w przemyśle
Efektywność energetyczna w przemyśle będzie zyskiwać na znaczeniu w najbliższych latach, napędzana przez kilka kluczowych trendów:
Digitalizacja i Przemysł 4.0
Inteligentne fabryki wykorzystujące Internet Rzeczy (IoT), sztuczną inteligencję i analizę dużych zbiorów danych (Big Data) będą w stanie osiągnąć bezprecedensowy poziom optymalizacji energetycznej. Cyfrowe bliźniaki procesów produkcyjnych pozwolą na symulację i testowanie różnych scenariuszy operacyjnych bez ryzyka dla rzeczywistej produkcji.
Elektrofikacja procesów przemysłowych
Wiele procesów przemysłowych, które tradycyjnie wykorzystywały paliwa kopalne, jest stopniowo zastępowanych technologiami elektrycznymi. W połączeniu z rosnącym udziałem odnawialnych źródeł energii w miksie energetycznym, elektryfikacja pozwoli na znaczącą redukcję śladu węglowego przemysłu.
Integracja z inteligentnymi sieciami energetycznymi
Elastyczne zarządzanie zapotrzebowaniem na energię (Demand Side Response) umożliwi przedsiębiorstwom przemysłowym aktywne uczestnictwo w bilansowaniu sieci elektroenergetycznej. Zakłady będą mogły dostosowywać swoje zużycie energii do aktualnej sytuacji w sieci, otrzymując za to wynagrodzenie od operatorów systemów przesyłowych.
Podsumowanie
Efektywność energetyczna stanowi ogromną szansę dla polskiego przemysłu na poprawę konkurencyjności i zrównoważony rozwój. Systematyczne podejście do zarządzania energią, inwestycje w nowoczesne technologie i budowanie świadomości energetycznej pracowników mogą przynieść znaczące korzyści finansowe przy jednoczesnym ograniczeniu negatywnego wpływu na środowisko.
W obliczu rosnących cen energii i coraz bardziej wymagających regulacji środowiskowych, efektywność energetyczna przestaje być opcją, a staje się biznesową koniecznością. Przedsiębiorstwa, które najszybciej dostosują swoje strategie i procesy do tych wyzwań, zyskają trwałą przewagę konkurencyjną na rynku.
Komentarze (6)
Jan Kowalski
10 marca 2025Bardzo praktyczny artykuł! W naszej firmie zaczynamy właśnie wdrażać system zarządzania energią. Czy może Pani polecić jakieś dobre narzędzia do monitoringu energetycznego dla średniej wielkości zakładu produkcyjnego?
Anna Nowak
9 marca 2025Zainteresował mnie temat białych certyfikatów. Czy mogłaby Pani napisać więcej o procedurze ich uzyskiwania? Jakie są minimalne progi oszczędności energii, aby kwalifikować się do tego programu?
Małgorzata Wiśniewska
9 marca 2025Dziękuję za pytanie, Anno. Aby uzyskać białe certyfikaty, oszczędność energii pierwotnej musi wynosić co najmniej 10 toe (ton oleju ekwiwalentnego) rocznie. Procedura obejmuje przeprowadzenie audytu efektywności energetycznej, złożenie wniosku do URE i - po realizacji przedsięwzięcia - audytu potwierdzającego. Planujemy niebawem osobny artykuł na ten temat.
Piotr Adamski
9 marca 2025Świetny artykuł! Zainteresował mnie temat odzysku ciepła odpadowego. W naszym zakładzie mamy sporo procesów generujących dużo ciepła, które obecnie jest marnowane. Jakie są typowe okresy zwrotu z inwestycji w systemy ORC?